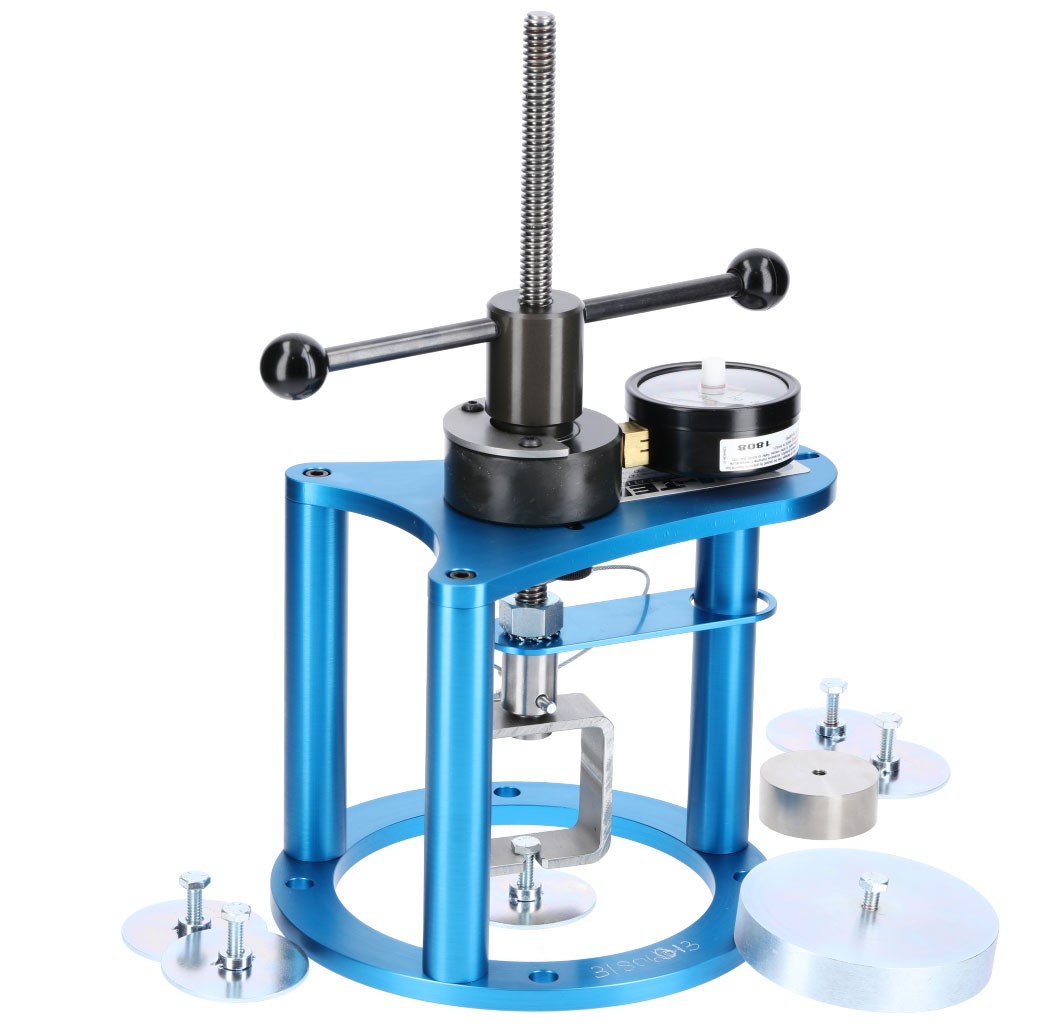
What is a pull tester? A detailed description of the instrument
Evolution of Pull Testers
Pull testers (or pull out testers) were originally designed to test the pull out resistance strength of roofing fasteners on commercial buildings.
During the last decade their use has become more widespread as building performance standards become higher and innovative construction techniques become more prevalent.
As buildings are subject to the continuous forces of wind, gravity, and their own weight, as well as extreme events such as earthquakes, hurricanes and floods, all manner of pull testing applications are possible and this has driven the industry to produce a wide range of pull testers suitable for each and every force testing scenario.
Today pull testers (whether digital or analog, manuals or motorized ) are used for performing direct tensile tests on roofing fasteners and other forms of construction. Their principal objective is to validate the withdraw resistance of fixings on substrates but they can also be used to validate and check for faulty fixing anchors in both new and existing construction.
Who can conduct a pull test?
To conduct a Pull Test, it is essential that the personnel involved are not just any engineers, but specifically those qualified to pull testing. These standards ensure that the operators are highly skilled and knowledgeable, capable of providing accurate readings following the test. This adherence to rigorous qualification criteria guarantees that safety is upheld during the testing process, reflecting the evolution of pull testers from simple tools to complex instruments that require a specialized understanding to operate effectively.
Understanding who can operate these sophisticated tools is as important as understanding the tools themselves. This ensures that every Pull Test is performed with precision, maintaining the integrity and safety of construction projects.
Why is Pull Testing important?
Pull testers (or pull out testers) were originally designed to measure the maximum load that a material or product can withstand before failing. This type of testing is crucial in industries such as construction, manufacturing, and quality control to ensure that products meet safety standards and perform as expected under stress and tension.
Beyond merely measuring capacity, pull testing is integral to preventing structural failures. Heavy loads and a lack of weather resistance are primary factors that lead to the deterioration of materials, particularly metals. By simulating these stresses, pull testing helps identify potential weaknesses before they can cause real-world issues.
The significance of implementing pull testing can't be overstated. It ensures that structures won’t collapse unexpectedly when erected, safeguarding against catastrophic outcomes. Essentially, this rigorous testing protocol is not just about compliance with safety standards—it's about saving lives by preemptively addressing potential failures.
In summary, pull testing acts as a critical checkpoint in the lifecycle of a product or structure, offering a vital assessment that helps ensure safety and reliability for the end users. By incorporating such tests before installation, industries can avoid severe accidents and enhance the durability of their constructs, thereby securing both functionality and public trust.
Pull Tester Components
Various physical components combine to make either a digital or analog pull tester the tool to be trusted for tests on fixtures, screws, fasteners, anchors, foam and membranes.
Force Sensor
A force sensor is the more important component of a pull tester. Capacities can be 300lbs, 1000lbs, 2000lbs, 4000lbs, and 6000lbs and are available to cover most, if not all, construction pull testing applications.
COM-TEN uses hydraulic force sensors and offers an extensive range of them. These sensors accept some misalignment without losing accuracy and will support shocks when a sample break occurs.
Readout
The two most common readouts are digital and analog.
* Digital Readout:
In Digital Readout the applied force can be read directly on the screen, and the force is held.
The operator needs to press the zero key after a test. The readout is assembled with the force sensor and both are calibrated.
* Analog Readout:
In analog readout a needle and red arrow points to the peak pull out force being applied. Operators need to return the needle to zero after a test.
This traditional type of basic readout is still sought after by professional testers.
Gauge
When assembled, the force sensor and the readout are together called the gauge and it\'s placed on the frame.
All COM-TEN gauges and frames are compatible. One frame can be used with several different gauge types to facilitate operators who have several types of tests to perform, including tests requiring the use of either a low force gauge or the use of a stronger gauge.
Frame
COM-TEN provides a 3 legs frame, supported by a large round base that weighs under a pound and is strong, being able to support over 20 000 lbs during validation tests.
Its base avoids damaging surfaces while a test is performed and the pulling force is applied to the roof surface. It size is designed to provide stability during tests and a good upright position for the force applied with easy access to the fastener head.
For special applications COM-TEN provides narrow frames, saddles, and extended frames and in case of particularly unlevel surfaces adjustable support feet are available.
Powerscrew
The power screw is the device that pulls the sample. A 4” travel distance allows freedom for placing a lifter foot in the right position.
COM-TEN testers have a fine thread screw in order for the operator turning the handle to have a smooth, easy movement.
Connector
The connector allows a lifter foot to be assembled with the power screw. As operators face a wide range of testing situations it is important to be able to change a lifter foot quickly and easily.
For this reason all COM-TEN pull testers have a connector that has a quick disconnect pin designed to accept all COM-TEN lifter feet.
Lifter Foot
All pull testers use a lifter foot (gripping fixture) to attach themselves to a fastener inserted under a fixture head. Drive-in light weight concrete fasteners and roofing screws are among the most common fasteners tested and specific lifter feet are used for each of these applications. Adhesion fixtures are also available to test adhesion strengths of glue and resin bonded materials and surfaces.
COM-TEN has designed a large family of compatible lifter feet which can be used with all pull testers.
Carrying case
All pull testers are delivered in a strong ‘COM-TEN tool box’ which is easy to carry on a vehicle and on a roof.
These plastic cases protect the instrument from shocks and a foam lining keeps the pull tester in the right position during transportation.
A small additional compartment is provided for other accessories on the top of the box.
How COM-TEN pull tester packages can assist with pull testing
At Streval, we specialize in anchor testing, ensuring your projects meet the highest safety and structural standards. COM-TEN has designed specific packages, including pull testers and relevant lifter feet suitable for all types of industry specs, and can provide customized kit assemblies, including frame, gauge and lifter feet, if none of the standard packages are suitable for to your specific needs.
Here's how we can help:
- Pull testers are made in Florida: our facility includes machine shop, assembly line and calibration bench to proudly provide continuously improved quality instruments to its US and foreign customers.
- We have it in stock: most of our pull tester are in stock and ready to be shipped for your next job.
- Certificate of calibration: All our pull testers are delivered with a certificate of calibration to help you achieve full compliance with industry standards and minimize risks.
Linked products
Pull-out-testing-equipment-for-Roofing-industry
EXTRACTOR D : Digital Pull Tester for screws, anchors, bolts- Full set of accessories for testing fasteners
- Display peak force ...
test-equipment-for-adhesion-tests-on-membrane-or-spf-in-construction
ADHOR D : Digital adhesion tester with disposable discs- Measure pull out strength between two layers after a repair or new work ...